FINISHING OPTIONS
PAINT
Paint may be defined as a thin layer of plastic film containing resin, binder, and pigment that is applied to the surface of an object to provide protection. Once the paint is applied it is allowed to cure, which causes the product to solidify, become harder, improve adhesion, change gloss and other physical characteristics. Paint coatings can be classified by function, curing system, volatile components, and resin system.
The primary component of paint is referred to as the resin. The type of paint comes from the resin system – Polyvinylidene Fluoride (PVDF), Polyester, Acrylic, Polyurethane or Epoxy. It is not uncommon for a coating to contain several resins, which help the coating perform to specific requirements. The fluoropolymer finish is applied in a two-coat, three-coat and four-coat application depending upon which finish color is being applied to the aluminum. Two-coat finishes consist of a primer coat and a color coat. Three-coat finishes consist of a primer coat, a color coat and a clear coat. Four coat finishes consist of primer coat, a barrier coat, a color coat and a clear coat.
Meets AAMA 2605 specifications for paint.
Strengths of Paint:
- Available in a vast array of colors and types.
- Can be made to meet the precise requirements of each project, either color or durability.
- Used to protect aluminum and maintain the structural integrity of the aluminum.
ANODIZING
Anodizing is an electrochemical process that converts a metal surface into a decorative, durable, corrosion-resistant, anodic oxide finish. Aluminum is ideally suited to anodizing.
The anodic oxide structure originates from the aluminum substrate and is composed entirely of aluminum oxide. This aluminum oxide is not applied to the surface like paint or plating, but is fully integrated with the underlying aluminum substrate, so it cannot chip or peel. It has a highly ordered, porous structure that allows for secondary processes such as coloring and sealing.
Anodizing is accomplished by immersing the aluminum into an acid electrolyte bath and passing an electric current through the medium. A cathode is mounted to the inside of the anodizing tank; the aluminum acts as an anode, so that oxygen ions are released from the electrolyte to combine with the aluminum atoms at the surface of the part being anodized. Anodizing is, therefore, a matter of highly controlled oxidation—the enhancement of a naturally occurring phenomenon. This process successfully combines science with nature to create one of the world’s best metal finishes.
The resulting finish, depending on the process, is the second hardest substance known to man, second only to the diamond.
Meets AAMA 611 specifications for anodizing.
Strengths of Anodizing
- Color stability
- Hardness, compared to a sapphire
- Anodize protects and maintains the structural integrity of the aluminum
- Non- hazardous, produces no harmful or dangerous by-products
- Ease of maintenance.
Weaknesses of Anodizing
- Limited color selection. Because of the chemicals used in the anodizing process, you are greatly limited on the color selection for your next project or product.
- Anodizing does not offer you the extended warranties as Superior Pigmented Painted Products.
- Touch-up of anodized product that is severely damaged in your shop or the field is more noticeable than air dry touch up paint for painted products.
The Anodizing Process
- Pre-Treatment: Cleaning is done in a non-etching, alkaline detergent heated to approximately 145 degrees Fahrenheit. This process removes accumulated contaminants
and light oils. - Rinsing: Multiple rinses, some using strictly de-ionized water, follow each process step.
- Etching (Chemical Milling): Etching in caustic soda (sodium hydroxide) prepares the aluminum for anodizing by chemically removing a thin layer of aluminum. This alkaline bath gives the aluminum surface a matte appearance.
- Desmutting: Rinsing in an acidic solution removes unwanted surface alloy constituent particles not removed by the etching process.
- Anodizing: Aluminum is immersed in a tank containing an electrolyte having a 15% sulfuric acid concentration. Electric current is passed through the electrolyte and the aluminum is made through the anode in this electrolytic cell; the tank is the cathode. Voltage applied across the anode and cathode causes negatively charged anions to migrate to the anode where the oxygen in the anions combines with the aluminum to form aluminum oxide (Al2O3).
- Coloring: Anodic films are well suited to a variety of coloring methods including absorptive dyeing, both organic and inorganic dyestuffs, and electrolytic coloring, both the Sandocolor® and Anolok® processes.
- Sealing: In all the anodizing process, the proper sealing of the porous oxide coating is absolutely essential to the satisfactory performance of the coating. The pores must be rendered non-absorbent to provide maximum resistance to corrosion and stains.
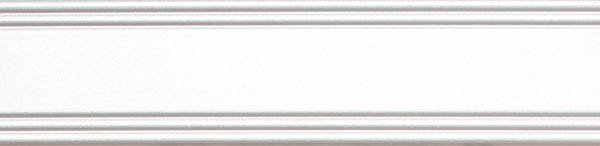
Clear Anodized ANO-215 or ANO-204
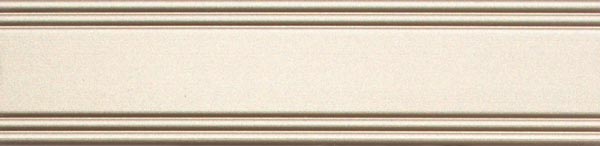
Champagne ANO-300
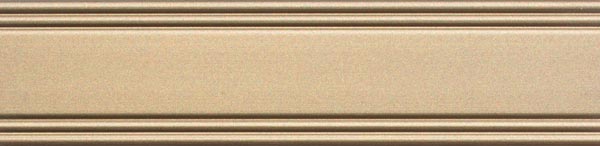
Light Bronze ANO-301
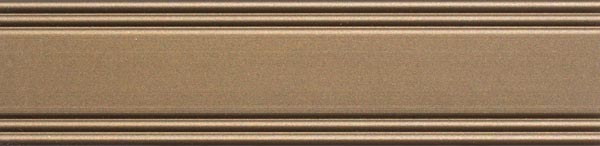
Medium Bronze ANO-302
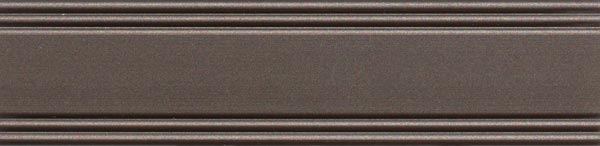
Dark Bronze ANO-303
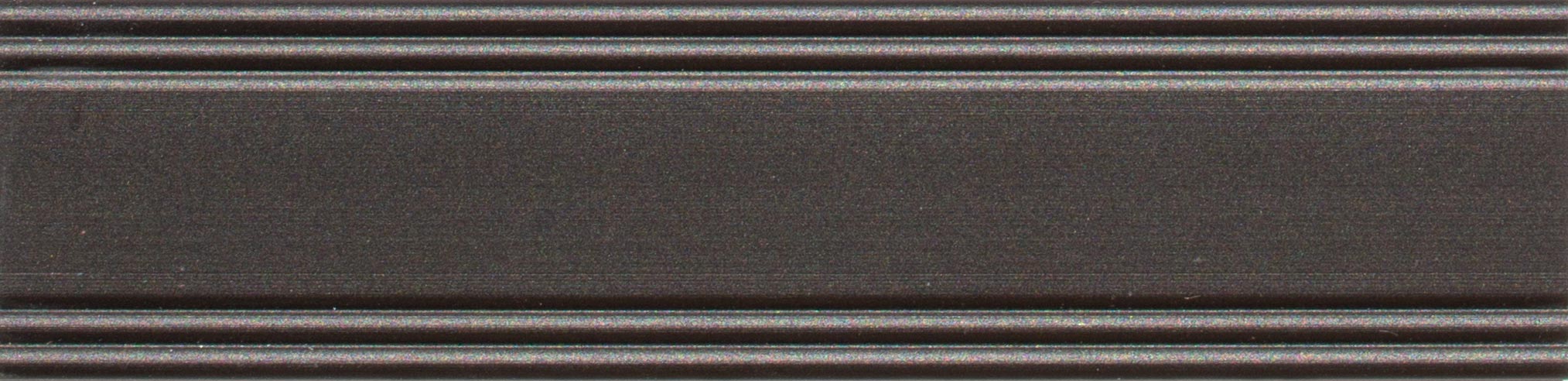
Extra Dark Bronze ANO-304
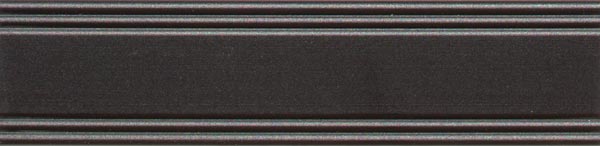
Black ANO-305
Anodized finishes are subject to color range due to the dipping process.
POWDER COATING
A dry finishing process that takes finely ground pigment and resin particles that are electrostatically charged and sprayed onto electrically ground parts.
Powder Coating is an advanced method of applying a decorative and protective finish to aluminum and other materials. The powder is a mixture of finely ground particles of pigment and resin, which is sprayed onto a surface to be coated. The charged powder particles adhere to the electrically grounded surface until heated and fused into a smooth coating. The result is a uniform, durable, high quality and attractive finish.
Strengths of powder coating:
- More durable – more resistant to chipping, scratching, fading and wear than other finishes.
- Protects the environment – contains no solvents and releases negligible amounts, if any, of volatile organic compounds (VOCs), found in most liquid finishes.
Weaknesses of powder coating:
Acurlite’s finisher of choice is LINETEC!
Take the next step
Contact Acurlite to discuss your project.